Referenz: Retrofit Niet- & Schweißautomat
Als erstes Retrofit-Projekt der eaw Relaistechnik sollte ein Niet- & Schweißautomat aus unserem eigenen Maschinenpark vollumfänglich modernisiert werden. Ziel dieses ersten Retrofit-Projekts war einerseits die vollständige Modernisierung der Anlage, andererseits der Aufbau und die Validierung von Know-How, um dem technischen und wirtschaftlichen Anspruch solcher Projekte gerecht werden zu können.
Eike Kammer, Project Manager Retrofit
+49 (0) 3375 2131-155
E.Kammer@eaw-relaistechnik.de
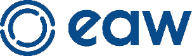
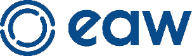
Problemstellung
Als Herzstück der Relaisfertigung produziert die Anlage bereits seit 1975 Kontaktfedern für die mechanischen Relais der EAW. Eine umlaufende Werkzeugkette führt dabei im drei Sekundentakt Federbleche entlang verschiedener Bearbeitungsstationen. An diesen werden den Federblechen Nietschaltstücke zugeführt und vernietet sowie ein Kontaktmesser angeschweißt. Abschließend werden die fertigen Kontaktfedern gebogen und sortiert.
Der jahrzehntelange Betrieb ist natürlich nicht spurlos an der Anlage vorbeigegangen. Im Laufe der Zeit verschlechterte sich die Qualität zusehends, Stillstände häuften sich und Ersatzteile waren in vielen Fällen nicht
mehr verfügbar. Die veraltete Schweißtechnik ließ sich kaum noch einstellen, sodass neue Materialien nicht zufriedenstellend bearbeitet werden konnten. Weiterhin war der Prozess mittlerweile so instabil, dass ein ständiger Eingriff nötig war und die Anlagenbediener während der Produktion gänzlich blockiert waren.
Hauptmotivation, um hier tätig zu werden, war jedoch das nicht mehr kalkulierbare Risiko eines irreparablen Ausfalls der Steuerungstechnik sowie, dass die Anlage nicht mehr den aktuellen Anforderungen an die funktionale Sicherheit genügte.
Durchführung
Mechanik & Oberflächenaufbereitung
Trotz einer langen Liste an Problemen befand sich die solide Mechanik der Anlage in einem guten Zustand, wodurch diverse Komponenten weiter genutzt werden konnten. Die Anlage wurde komplett demontiert und jedes Bauteil analysiert, bewertet und aufgearbeitet. Oberflächen wurden gereinigt und pulverbeschichtet, beschädigte Komponenten neu gefertigt.
Elektro- & Automatisierungstechnik
Die antiquierte URSALOG 4000-Steuerung wurde durch eine aktuelle Siemens-Steuerung + HMI ersetzt. Als Steuerungskonzept wurde eine Zustandsmaschine auf Basis der OMAC PackML implementiert, welche sich nicht nur für Verpackungsmaschinen eignet. Durch den Einsatz der neuen Automatisierungstechnik können nun alle relevanten Prozess- und Fertigungsdaten erfasst, visualisiert und über eine I4.0-konforme Schnittstelle (OPC UA) zur weiteren Verarbeitung angeboten werden.
Das fehleranfällige Nockenschaltwerk zur Erkennung der Kettenposition wurde durch einen präzisen Absolutwertgeber ersetzt, wodurch sich entscheidende Vorteile der Prozessüberwachung ergaben. Der über die Zeit entstandene Misch-Masch an unterschiedlichen Sensoren wurde durch den Einsatz von Standardkomponenten abgelöst, was eine gewisse Herstellerunabhängigkeit bei der Ersatzteilbeschaffung garantiert.
Die veraltete Phasenanschnitts-Schweißanlage wurde gegen leistungsfähige Mittelfrequenztechnik ersetzt. Die Möglichkeit der präzisen Überwachung und Regelung der Schweißprozesse ermöglichte eine deutliche Steigerung der Schweißqualität und Prozessstabilität. Ein weiterer Vorteil der neuen Schweißtechnik liegt darin, dass die Anlagenbediener selbst keine Parametrisierung mehr vornehmen müssen, sondern lediglich die gewünschte Produktart auswählen und den Produktionsprozess starten.
Neben der gesamten elektrotechnischen Ausstattung wurde auch die Pneumatik erneuert und auf den aktuellen Stand gebracht. Der Einsatz moderner und effizienter Komponenten verringert maßgeblich den Energiebedarf der Anlage und führt zu einer deutlich verbesserten Wartbarkeit in allen Bereichen.
Risikobeurteilung & Technische Dokumentation
Aufgrund des hohen Alters verfügte die Anlage über keine CE-Kennzeichnung. Auch die zum damaligen Zeitpunkt der Konstruktion geltenden Anforderungen entsprachen in vielen Fällen nicht mehr den aktuell gültigen. Auf dieser Grundlage musste eine Gefährdungsbeurteilung durchgeführt und die Anlage entsprechend der geltenden Richtlinien ertüchtigt werden, dazu gehörte auch die Erstellung einer vollständigen und rechtssicheren technischen Dokumentation. Die Dokumentation der Elektro- und Fluidtechnik erfolgte mittels E-Plan P8, technische Zeichnungen wurden mit Solid Edge erstellt. Im Ergebnis konnte die CE-Konformität verifiziert werden und wir bedenkenlos die Hersteller-verantwortung übernehmen.
Ergebnisse im Überblick
Dem Kunden, in diesem Fall unsere eigene Fertigung, konnte im Ergebnis eine praktisch neue Anlage übergeben werden. Die konkreten Ergebnisse dieses Retrofit-Projekts sollen abschließend noch einmal hervorgehoben werden.
- optisch und mechanisch generalüberholte Anlage
- Neue elektrotechnische Ausstattung und Automatisierungstechnik
- Neue Fluidtechnik
- Vollständige und rechtssichere Technische Dokumentation
- Erfolgreiche Risikobeurteilung & CE-Zertifizierung
- Langfristige Ersatzteilversorgung
- I4.0-konforme Schnittstelle zur Integration in SCADA bzw. ERP-System
- Mehr als 50% Platzersparnis im Vergleich zur „Alt- Anlage“ (Integration von Steuerung und Schweißtechnik in den Maschinentisch)
- Energieeinsparung im Betrieb durch effiziente Pneumatik und Schweißtechnik
- Deutliche Steigerung der Qualität der zu fertigenden Produkte